Last December, Hoist Magazine published an article about the new trends regarding the developments in the field of intelligent manufacturing in high end industries, emphasizing the machine to machine and machine to product communication.
LOAD LIMITER EVOLVED
A company that is moving quickly on this approach is Spain’s GH Cranes & Components, which has evolved its load limiter technology into its CoreBox which is standard on all new products. “Essentially the CoreBox has evolved into a data logger that is collecting the data from the operation of the cranes,” says Pablo Pedrós Solano, director of engineering and research and development at the company. This data includes information about the load lifted at each time—the overloads, the temperature of the motors and information from several alarms, among others. “The CoreBox is the product collecting the data and then transferring it to different platforms like an App or a PC or the Global Service centre here at GH.”
That the CoreBox now comes as standard highlights the firm’s commitment to future smart technology and means that the customer doesn’t have to buy the device as an addon. One of the biggest benefits, says Solano, is intelligent maintenance: “Many maintenance contracts [are based on periodic] preventive maintenance. With the huge amount of data that we are collecting, we can go from preventive to predictive maintenance [based on actual use]. That is a challenge for the industry—to balance the maintenance mix towards predictive actions.”
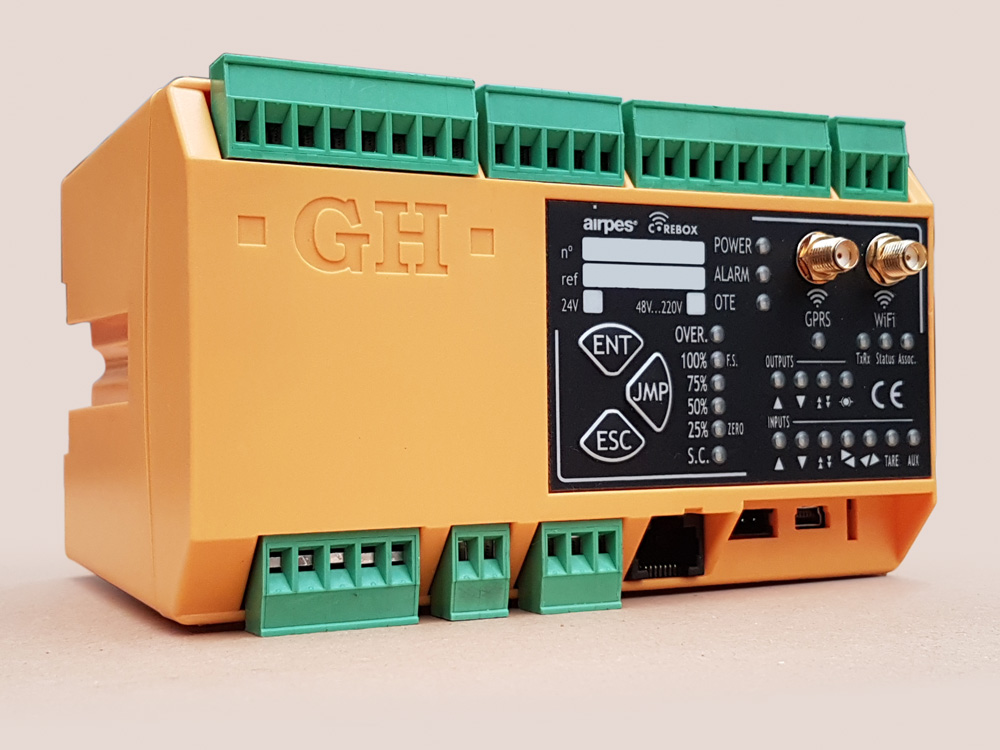
Complementing this move to intelligent maintenance, GH Cranes & Components has also launched a new customer portal dedicated to maintenance management designed to be a direct link between the customer and the Global Service centre.
“The cloud-based software allows us to get all of the incidents and tasks that customer sends directly,” says Solano. “It will improve the lead time for fixing or materials requirements. It also grants access to the customer in order to review the historical maintenance data and technical information of the crane.”
The system is also linked to the company’s enterprise resource planning system, allowing the customer to schedule in their maintenance requirements directly. “Very few companies have implemented this gateway,” says Solano.
The firm provides customers with a number of options for accessing the information from the CoreBox data logger: 3G, GPRS, wifi, and local USB connection. It has also developed Apps and software to enable connection from tablets or smartphones as well as the PC or radio remote controls.
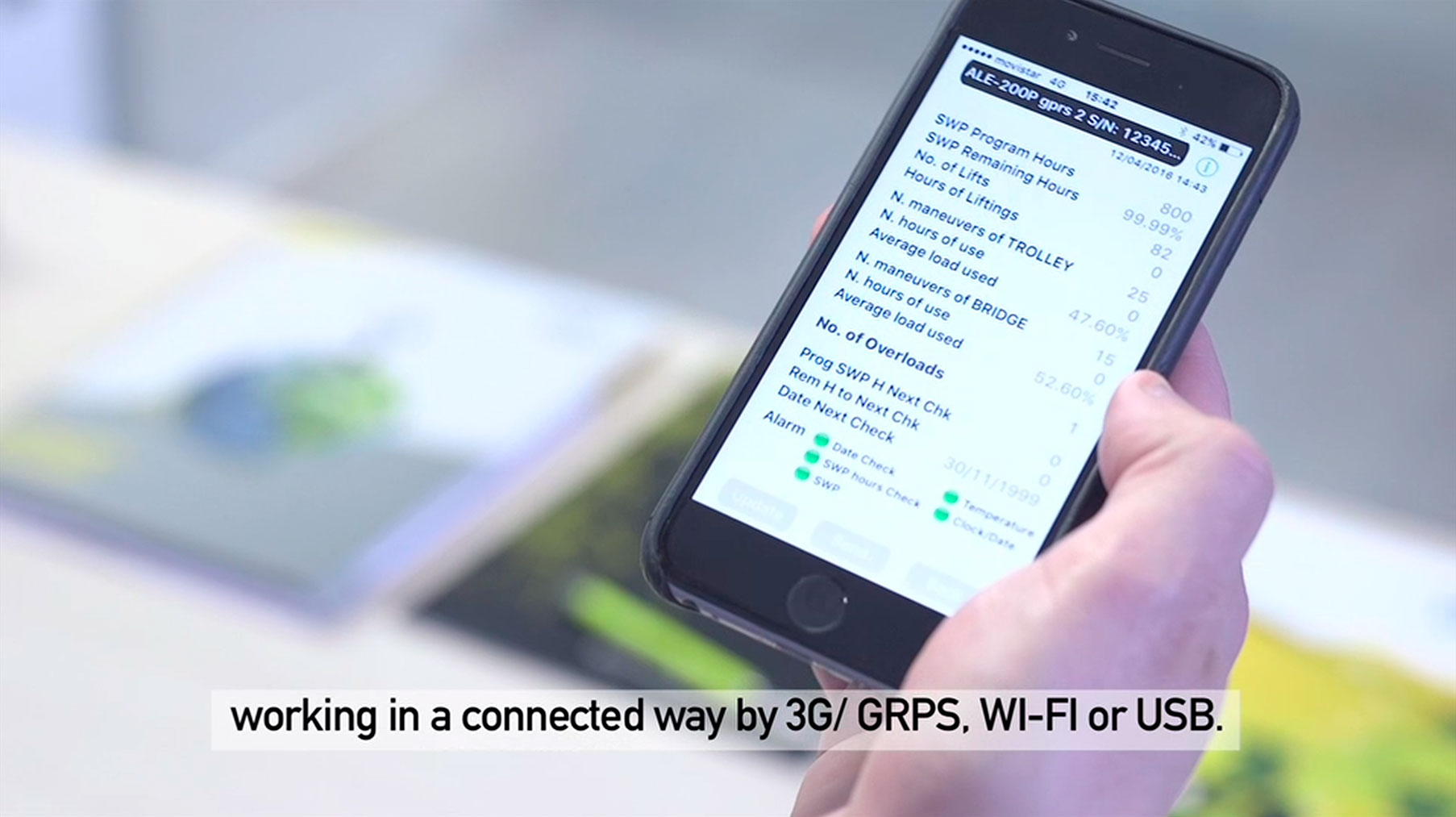
A key advantage of the collection and sharing of data is that it can be used by manufacturers to update their products more effectively. It also means investment in new processing capacity. “We will need to be on a strong platform to allow our customers to have all of their data ready and available. But also that the data is available to us to keep updating and improving our products because the research and development department will have valuable information about the way that our cranes are used,” says Solano.
Access to this data is one of the challenges for the industry to contend with and Solano points out that GH will only be able to access this with the customer’s permission.
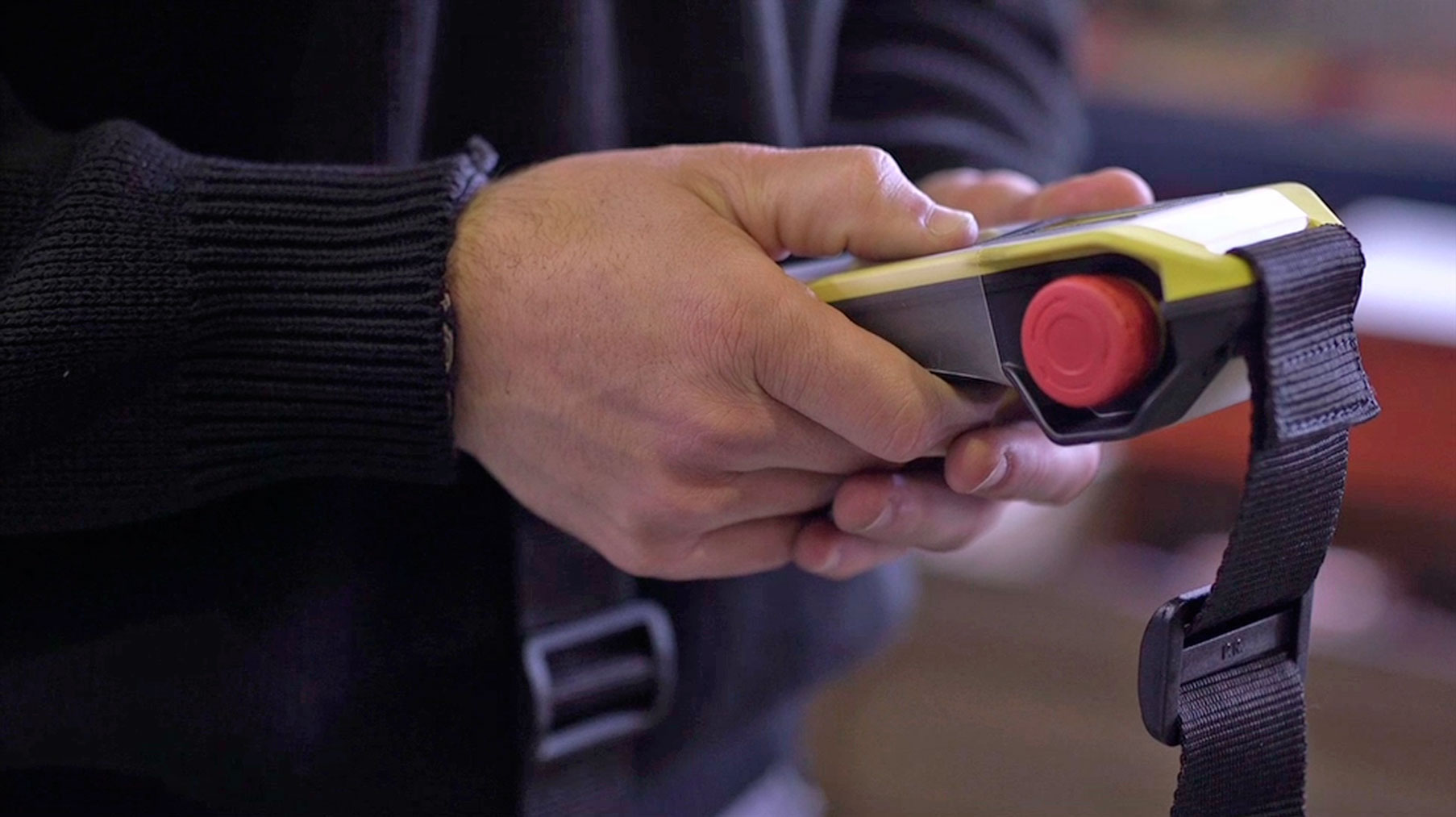
UK manufacturer Street Crane says that it can provide wifi access to the data from its safe working period (SWP) monitor, which has a data logging function, but so far it is yet to see demand from customers. “We haven’t installed it with a communications module yet because a lot of people are concerned about network security. If you have that simple device that is wifi enabled it is at risk if it is connected to your network, so they are just standalone units at the moment,” says Chris Lindley- Smith, director at the company.
Traynor says: “Cyber incidents are real and a challenge for industry but it is definitely a challenge that can be met and there are lots of different ways to address that. It comes down to things like auditing equipment, who is authorised to get to the information. How and who can work with it, ensuring the integrity of the data, where information has gone and who has had access to it.”
This could see the need for nondisclosure agreements to ensure that information is protected, says Thomas Kraus, support centre director for Stahl CraneSystems, which is owned by Konecranes: “For sure that with this information you can give the customers a better service, there is no question, but you need access to the information and this must be solved first.”
Link to complete article «www.hoistmagazine.com»